Titanium Powder for 3D Printing
Real-World Applications of Titanium 3D Printing
Titanium, with its unique blend of strength, lightness, and biocompatibility, has found a home in various industries. When combined with the design freedom and efficiency of 3D printing, it opens up a world of possibilities. Let’s explore some real-world applications of this powerful duo.
The Perfect Blend: Titanium Powder and 3D Printing for Aerospace Innovation
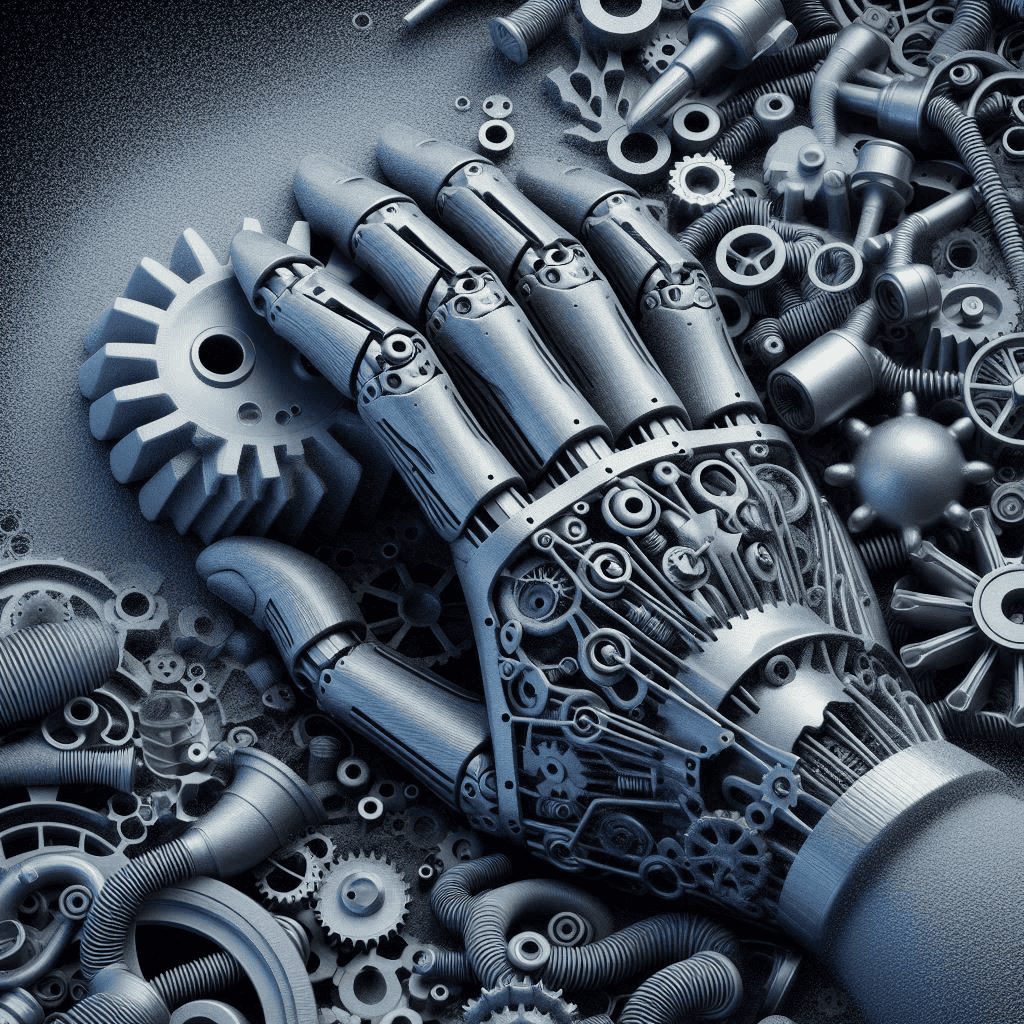
The aerospace industry is at the forefront of technological advancement, constantly pushing the boundaries of what is possible. Central to this innovation is the perfect marriage of materials science and manufacturing processes. One such dynamic duo is titanium powder and 3D printing.
Why Titanium?
Titanium is a metal celebrated for its exceptional properties. It’s incredibly strong yet remarkably lightweight, making it an ideal material for aerospace applications. Its resistance to corrosion and extreme temperatures further solidifies its status as a go-to choice for aircraft and spacecraft components.
The Role of 3D Printing
Traditional manufacturing methods often fall short when it comes to the complex geometries and intricate details required for aerospace components. Here’s where 3D printing shines. By melting and fusing titanium powder layer by layer, it allows for the creation of parts with unparalleled precision and complexity.
A Perfect Match
The combination of titanium powder and 3D printing offers a plethora of advantages for the aerospace industry:
- Weight Reduction: Aerospace engineers are constantly striving to reduce aircraft weight to improve fuel efficiency and performance. Titanium’s inherent lightness, combined with the ability of 3D printing to create complex, hollow structures, results in components that are significantly lighter than their traditionally manufactured counterparts.
- Enhanced Performance: 3D printing enables the creation of parts with optimized internal structures, leading to improved strength-to-weight ratios. This translates to enhanced performance and durability for aircraft components.
- Reduced Lead Times: Traditional manufacturing processes can be time-consuming and involve multiple steps. 3D printing offers significantly shorter lead times, allowing for faster prototyping and production of aerospace components.
- Complex Geometries: Aerospace components often feature intricate shapes and designs. 3D printing excels at producing these complex geometries with precision, eliminating the need for assembly and reducing the risk of errors.
- Consolidated Parts: By combining multiple components into a single 3D-printed part, manufacturers can reduce the number of assembly points, saving time and weight.
Real-World Applications
From aircraft engines to satellite components, titanium 3D printing is making waves in the aerospace industry. Some notable examples include:
- Engine Components: Turbocharger and turbine blades manufactured using titanium powder offer improved performance and durability.
- Aircraft Frames: Lightweight and strong titanium frames are being developed to reduce overall aircraft weight.
- Satellite Structures: Titanium 3D-printed components are being used to create more resilient and efficient satellites.
- Spacecraft Parts: Rockets and spacecraft are benefiting from the use of titanium 3D-printed parts, as they can withstand the extreme conditions of space.
The Future is Bright
As technology continues to advance, we can expect even more groundbreaking applications of titanium powder and 3D printing in the aerospace industry. From developing innovative propulsion systems to creating revolutionary spacecraft designs, the possibilities are endless.
The perfect blend of titanium powder and 3D printing is undoubtedly propelling the aerospace industry into a new era of innovation, efficiency, and sustainability.
The Perfect Blend: Titanium Powder and 3D Printing for Medical Marvels
The convergence of advanced materials and innovative manufacturing techniques is revolutionizing healthcare. At the forefront of this medical renaissance is the extraordinary combination of titanium powder and 3D printing. This dynamic duo is reshaping patient care by delivering customized, high-performance medical solutions.
The Power of Titanium
Titanium is a remarkable metal renowned for its exceptional properties. It is incredibly strong yet remarkably lightweight, making it an ideal material for medical implants. Additionally, titanium is biocompatible, meaning it is well-tolerated by the human body, reducing the risk of rejection.
The Precision of 3D Printing
3D printing, also known as additive manufacturing, offers unparalleled precision and flexibility in creating complex objects. When combined with titanium powder, it enables the fabrication of intricate medical implants tailored to individual patient needs.
Transforming Patient Care
The synergy between titanium powder and 3D printing is transforming patient care in several ways:
- Customized Implants: Unlike traditional, off-the-shelf implants, 3D-printed titanium implants can be precisely designed to match a patient’s unique anatomy. This level of customization enhances implant fit, stability, and overall patient outcomes.
- Complex Geometries: 3D printing allows for the creation of intricate and complex implant designs that would be impossible to manufacture using traditional methods. This opens up new possibilities for treating challenging medical conditions.
- Reduced Surgical Time: Customized implants often require less invasive surgical procedures, leading to shorter recovery times and reduced patient discomfort.
- Improved Functionality: 3D-printed titanium implants can be designed to optimize functionality and performance. For example, hip implants can be designed to mimic the natural bone structure, improving mobility and reducing the risk of dislocation.
- Accelerated Development: 3D printing enables rapid prototyping and iteration, accelerating the development of new medical devices and treatments.
Real-World Applications
The impact of titanium 3D printing is evident in various medical fields:
- Orthopedics: Customized hip, knee, and spinal implants are revolutionizing orthopedic surgery.
- Dentistry: Dental implants, crowns, and bridges can be created with precision and accuracy.
- Craniomaxillofacial Surgery: Complex facial reconstructions are becoming more achievable with 3D-printed titanium implants.
- Trauma Surgery: Customized plates and screws can be rapidly produced to treat bone fractures.
The Future of Medical Innovation
The potential of titanium powder and 3D printing in healthcare is vast. As technology continues to advance, we can anticipate even more groundbreaking applications, such as:
- Bioresorbable implants: Developing implants that gradually dissolve as the bone heals.
- Organ and tissue engineering: Creating artificial organs and tissues using 3D-printed scaffolds.
- Personalized medicine: Tailoring treatments to individual patients based on their genetic makeup and medical history.
The fusion of titanium powder and 3D printing is undoubtedly reshaping the landscape of healthcare, offering hope and improved outcomes for countless patients.
The automotive industry is undergoing a transformative shift, driven by the relentless pursuit of performance, efficiency, and sustainability. At the heart of this revolution is the strategic use of advanced materials, and titanium powder is emerging as a key player.
The Allure of Titanium
Titanium is a metal celebrated for its exceptional properties: it’s incredibly strong yet remarkably lightweight, making it an ideal material for automotive applications. Its resistance to corrosion and extreme temperatures further solidifies its status as a coveted choice for vehicle components.
The Role of Titanium Powder
Titanium powder, when combined with the precision of 3D printing, unlocks a world of possibilities for automotive manufacturers. This potent combination enables the creation of complex and lightweight components that were previously unattainable.
Revolutionizing Automotive Design
The automotive industry is leveraging titanium powder to push the boundaries of design and performance:
- Lightweight Components: Titanium’s inherent lightness, combined with the ability of 3D printing to create complex, hollow structures, results in components that are significantly lighter than their traditionally manufactured counterparts. This weight reduction translates to improved fuel efficiency and vehicle performance.
- Enhanced Performance: 3D printing enables the creation of parts with optimized internal structures, leading to improved strength-to-weight ratios. This translates to enhanced performance and durability for automotive components.
- Complex Geometries: Automotive components often feature intricate shapes and designs. 3D printing excels at producing these complex geometries with precision, eliminating the need for assembly and reducing the risk of errors.
- Consolidated Parts: By combining multiple components into a single 3D-printed part, manufacturers can reduce the number of assembly points, saving time and weight.
Real-World Applications
The automotive industry is already reaping the benefits of titanium powder 3D printing:
- Brake Calipers: Titanium brake calipers offer superior heat dissipation and weight reduction, enhancing braking performance.
- Engine Components: Titanium components can improve engine efficiency, power output, and durability.
- Chassis Components: Lightweight and strong titanium chassis components can enhance vehicle handling and responsiveness.
- Exhaust Systems: Titanium exhaust systems offer weight reduction, improved performance, and a distinctive sound.
Challenges and the Road Ahead
As technology continues to advance, we can expect to see even more groundbreaking applications of titanium powder in the automotive industry. From electric vehicles to high-performance sports cars, this powerful material is poised to drive innovation and shape the future of transportation.
Titanium Powder: Forging High-Performance Sports Equipment
The world of sports is constantly evolving, driven by the relentless pursuit of peak performance. Athletes demand equipment that is not just functional, but also provides a competitive edge. This is where the combination of titanium powder and 3D printing shines.
3D Printing: Tailoring for Champions
3D printing, also known as additive manufacturing, offers unparalleled precision and flexibility in creating complex objects. When combined with titanium powder, it enables the fabrication of custom sports equipment tailored to individual athletes. This technology allows for:
- Customized Fit: Every athlete is unique, and their equipment should be too. 3D printing allows for the creation of perfectly fitted equipment, enhancing performance and comfort.
- Optimized Performance: By understanding the specific needs of an athlete, engineers can design equipment with optimized performance characteristics, such as improved aerodynamics or energy return.
- Complex Geometries: Traditional manufacturing methods often struggle with complex shapes. 3D printing excels at creating intricate designs, leading to innovative and high-performance equipment.
- Lightweight Construction: Titanium’s inherent lightness, combined with the ability of 3D printing to create hollow structures, results in equipment that is both strong and lightweight.
High-Performance Applications
The potential applications of titanium powder and 3D printing in sports are vast. Some examples include:
- Cycling: Lightweight and aerodynamic frames, handlebars, and components.
- Motorsports: Helmets, chassis components, and protective gear with enhanced safety and performance.
- Golf: Club heads with optimized weight distribution and aerodynamics.
- Water Sports: Surfboards, kayaks, and other equipment with improved buoyancy and durability.
- Winter Sports: Skis, snowboards, and protective gear with enhanced performance in extreme conditions.
The Future of Sports Equipment
The combination of titanium powder and 3D printing is still in its early stages, but its potential is immense. As technology continues to advance, we can expect to see even more applications in the world of sports. From personalized equipment to revolutionary designs, the future of sports equipment is bright.
The perfect blend of titanium powder and 3D printing is set to redefine the performance boundaries in sports, empowering athletes to reach new heights.
Beyond the Obvious: Other Applications
The versatility of titanium 3D printing extends to other industries:
- Oil and gas: Corrosion-resistant components for harsh environments.
- Defense: Lightweight and durable equipment for military applications.
- Consumer goods: High-end equipments and luxury products.
Challenges and the Road Ahead
While titanium 3D printing offers immense potential, challenges such as high material costs and post-processing complexities need to be addressed. However, ongoing research and development are paving the way for overcoming these hurdles.
As technology continues to advance, we can expect to see even more groundbreaking applications of titanium 3D printing across various sectors. From the skies to the human body, this powerful combination is reshaping industries and improving our lives.